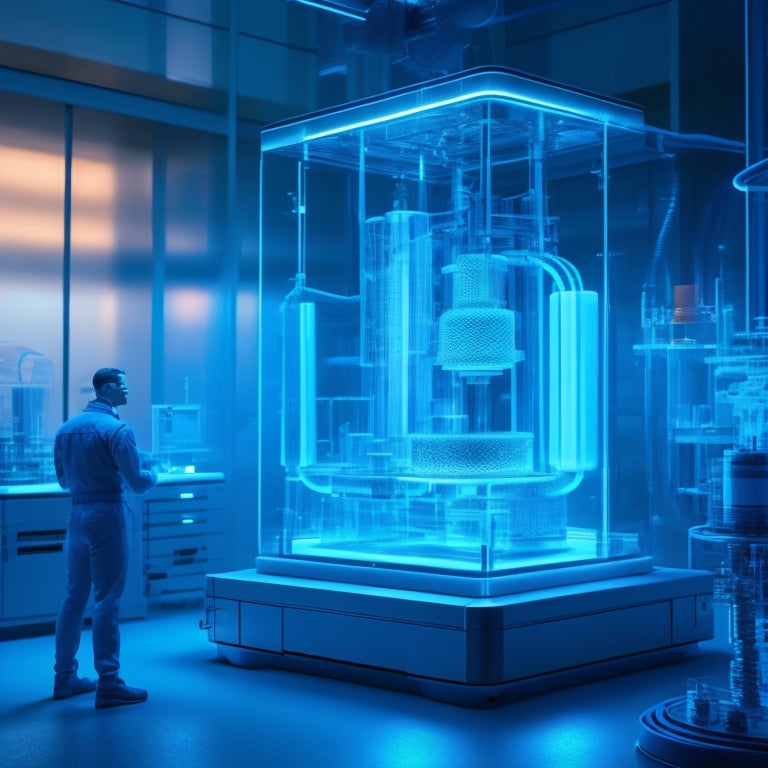
Unlocking the Secrets of Transparent 3D Printing
Share
I've spent countless hours perfecting transparent 3D prints, and I've found that heat control, material properties, and printing settings hold the key to achieving ideal clarity. Inconsistent material flow, often due to poor heat control, leads to imperfections and gaps. By fine-tuning nozzle temperature, printing speed, and material flow rate, I've been able to achieve seamless bonding and ideal material deposition. But it's not just about getting it right during printing – post-processing techniques like sanding and polishing are essential for maximizing transparency. By digging deeper into the nuances of material flow and printing settings, I've discovered even more secrets to achieving truly exceptional transparent prints.
Key Takeaways
• Proper heat control and material flow are crucial for achieving transparency in 3D printing, as inconsistencies can lead to gaps and imperfections.
• Balancing volume per second and nozzle temperature is vital for ideal material flow and transparency, and requires fine-tuning of printing settings.
• Post-processing techniques such as sanding with fine grit paper and applying polish finishes can enhance transparency and remove imperfections.
• Material properties and printing settings must be optimized for transparency, including adjusting infill settings, managing moisture, and referencing material data sheets.
• Fine-tuning extrusion multiplier, nozzle size, and printing speed can help achieve optimal print settings for transparent prints, with a recommended setting of 0.4 mm nozzle size and 15 mm/sec printing speed.
Material Properties and Printing
When it comes to achieving transparent 3D prints, I've found that getting the material properties and printing settings just right is essential, as it directly impacts the final print's clarity and quality.
One of the biggest extrusion challenges is ensuring consistent material flow, which can be achieved through proper heat control. If the material doesn't flow smoothly, it can lead to gaps and imperfections, compromising transparency.
To overcome this, I use an interlocking technique that allows the material to bond seamlessly, eliminating any potential gaps.
Transparency Optimization Techniques
I've found that balancing volume per second and nozzle temperature is key to achieving peak transparency in my 3D prints. This delicate balance guarantees that the material flows smoothly and consistently, resulting in a clear and transparent finish.
To optimize transparency, I follow these guidelines:
-
Temperature control: Adjust the nozzle temperature to make sure the ideal heat energy is applied to the material.
-
Speed adjustment: Fine-tune the printing speed to prevent overheating or under-heating, which can impact transparency.
-
Flow rate optimization: Balance the flow rate to achieve the perfect volume per second, ensuring consistent material deposition.
- Volume balance: Ensure the extruder is calibrated to deliver the correct volume of material, preventing under-extrusion or over-extrusion.
Post-Processing and Troubleshooting
By carefully sanding with fine grit paper, I can achieve a smooth finish that enhances the transparency of my 3D printed parts. This post-processing step is essential in removing imperfections on the outer surface, allowing the part to refract light more evenly.
I've found that sanding techniques borrowed from post-processing metal-filled filaments work well for transparent prints. After sanding, I apply polish finishes to achieve maximum transparency. It's amazing how a little elbow grease can transform an already impressive print into an exceptionally clear one.
Material Comparisons and Optimization
nGen clear, a popular choice for transparent 3D prints, shares similar printing requirements with HT clear, emphasizing the importance of maintaining ideal material flow to guarantee interlocking layers.
To achieve the best transparency, I focus on material comparisons and optimization.
Here are key factors to take into account:
-
Density optimization: Adjust infill settings to achieve the desired density, and experiment with slicer and flow settings for best results.
-
Moisture management: Make certain the spool is dry, and maintain temperatures below 100C to prevent moisture from affecting transparency.
-
Proper material flow and interlocking layers are essential for transparency.
- Reference material data sheets for density and adjust settings accordingly.
Achieving Optimal Print Settings
To achieve ideal print settings for transparent 3D prints, I begin by fine-tuning my extrusion multiplier to prevent under-extrusion, ensuring that the material flows and interlocks fully to prevent gaps.
Temperature control is essential, as it directly affects filament flow. I set my nozzle size to 0.4 mm, which provides the best balance between layer height and printing speed. Printing at 15 mm/sec with a 0.1 layer height allows for precise control over the material flow.
By balancing volume per second and nozzle temperature, I can achieve clear and transparent prints. I also adjust my printing speed to ensure the best temperature, as printing too hot or too cold can compromise transparency.
With these settings, I can achieve nearly fully transparent prints without the need for sanding.
Overcoming Common Printing Issues
When printing transparent parts, I've encountered several common issues that can compromise their clarity, including under-extrusion, warping, and layer shifting. To overcome these problems, I've developed a few strategies.
Here are some key troubleshooting steps:
-
Troubleshoot under-extrusion: Check for nozzle clogging and ensure proper extrusion multiplier settings to avoid under-extrusion.
-
Manage heat effectively: Ensure proper heat management to prevent warping and layer shifting.
-
Optimize layer adhesion: Adjust temperature and layer height settings to achieve the best layer adhesion.
- Monitor print speed: Adjust print speed to prevent layer shifting and guarantee smooth layer changes.
Unlocking Maximum Transparency
By fine-tuning my printing settings and material properties, I've been able to achieve remarkably clear and transparent parts, but I'm now focused on maximizing transparency in my 3D prints.
To access maximum transparency, I've found that transparency enhancement is essential. By optimizing my print settings, such as layer height, speed, and infill, I can achieve unparalleled print clarity.
Balancing volume per second and nozzle temperature is vital, as is adjusting speed for best temperature. I've also found that using rectilinear infill and ensuring proper extrusion multiplier helps prevent gaps and under-extrusion.
Frequently Asked Questions
Can I Use Transparent 3D Printing for Outdoor Applications?
I view UV resistance and weatherproofing as essential for outdoor applications, so I'd meticulously assess the material's properties and printing settings to guarantee my transparent 3D prints can withstand harsh environmental conditions without compromising their transparency.
How Do I Prevent Warping in Large Transparent Prints?
To prevent warping in large transparent prints, I guarantee proper bed adhesion by using a heated chamber with a temperature around 40°C, and a bed material that promotes adhesion, such as borosilicate glass or a PEI sheet.
Are There Any Food-Safe Transparent 3D Printing Materials?
I'm on the hunt for food-safe transparent 3D printing materials, and I've got my eyes on materials with certifications like FDA compliance, EU food contact regulations, and ROHS compliance to guarantee safety in food-related applications.
Can I Combine Transparent and Opaque Materials in One Print?
When combining transparent and opaque materials, I achieve material gradients by adjusting print layering, ensuring a smooth shift between materials, and maintaining precise temperature control to prevent warping or delamination.
What Are the Limitations of Transparent 3D Printing for Moving Parts?
I've found that transparent 3D printing for moving parts is limited by friction issues and material creep, which can lead to wear and tear, compromising the part's integrity and potentially causing safety hazards.
Related Posts
-
Family Harmony Achieved: Doral Home Renovation Unveiled
We designed our Doral home renovation around a simple yet powerful idea: that a unified, open space can bring our fam...
-
Deighton Associates Awarded for Excellence in Asset Management
You're likely curious about Deighton Associates' recent recognition for excellence in asset management. They've recei...